
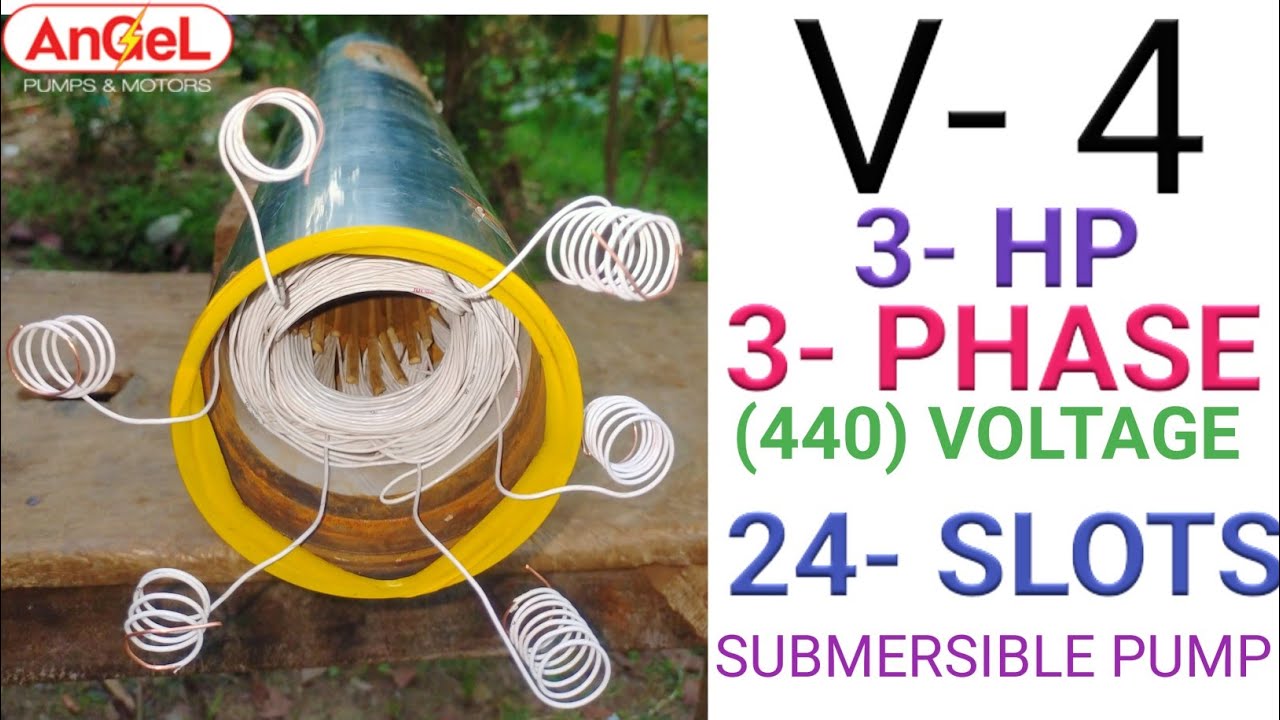
small motors,operating at ordinary supply voltages with a small number of slots having a large number of turns per phase may use single layer mush winding.Stator winding are almost always short pitched because of reduced copper weight and winding resistance as well as reduced leakage reactance and harmonic torque disturbances that results. The double layer winding is mostly used in medium size motors because of its greater ease of manufacture,assembly,and repair. The wound rotor motor are started by inserting resistance in the rotor circuit and therefore the stator winding can be connected in either star or delta as desired. The squirrel cage motors are usually started by star-delta starters and therefore their stators are designed for delta connections and six terminals are brought out to be connected to the starter. In a polyphase induction motor the stator winding is usually 3-phase winding which is usually supplied from 3-phase supply mains.The three phases of the winding can be connected in either star or delta depending upon the methods of starting used. Thickness of punching may varies from 0.35mm to 0.65mm. Carry the alternating flux which produces Hysteresis losses and eddy current losses.In order to reduce eddy currents and hysteresis loss in the stator core it is assembled of high-grade,low-electrical loss,silicon steel punchings.The stator of an induction motor is quite similar in construction to that of a 3-phase synchronous alternator or motor. To protect the inner parts of the machine and serve as a ventilating housing or means of guiding the coolant into effective channels.The frames should be strong and rigid as air gap length in an induction motor is very small.If the frame is not rigid ,the rotor will not remain concentric with stator giving rise to unbalanced magnetic pull. It is the outer body of the motor.The frame may be die cast or fabricated.The frames for medium and large machines are almost exclusively fabricated.Machines up to about 50 KW rating may have frame die cast in a strong silicon-aluminium alloy,sometimes with the stator core cast in.įor large motors of rating 250 KW to 10,000 KW,the frames are generally fabricated in the form of box type enclosures having detachable top cover.Frames are provided with feet by which they are fixed to the base plate. A frame to form the stator housing and carry the end covers bearings, and terminal box.Ĭonstruction of Three phase Induction motor 1.Frame:.A stiff shaft to preserve the very short air gap.A laminated rotor core carrying either a cage or polyphase winding, the latter with shaft-mounted slip rings polyphase winding ,the latter with shaft-mounted slip rings.A laminated stator core carrying a polyphase winding.The several features of induction motors are: They are widely used in electric motors in industry. That confirms that the permissible drive voltage must be reduced by the motor controller at stall, and probably also at startup.Įither their recommended controller will do this for you, or you'll have to actively measure the current and control the PWM duty cycle to stay within the motor's limits.Three phase induction motor are simple in construction as compared to DC Motorsor synchronous motor. It's not clear which motor from that page you are using, but the typical "performance" data on that page is unusual - it shows a "stall torque" that is only slightly higher than the torque at max power - and a much lower power dissipation at stall. start it at a much lower voltage (or with PWM at a much lower duty cycle (about 7%).
3PHASE MOTOR WINDING DRIVER
That also means the stall current at 28V is somewhere over 100A.Īs you suggest in a comment that you have a peak current limit of 7A (what imposes this limit?) that means your motor driver must soft-start the motor, i.e. That means the 0.26 ohm measurement you made is already across two (0.13 ohm) windings in series. First, you said it was a star wound motor with no neutral.
